The automotive industry is undergoing a massive transformation, and one of the most exciting innovations driving this change is 3D printing. Once considered a futuristic concept, 3D printing is now revolutionizing car manufacturing, design, and production. From prototyping and lightweight components to sustainability and cost savings, this technology is reshaping how vehicles are built. Let’s explore how 3D printing is impacting the automotive industry and what the future holds.
The Rise of 3D Printing in Car Manufacturing
3D printing, also known as additive manufacturing, allows manufacturers to create complex parts layer by layer using plastics, metals, and composites. Unlike traditional manufacturing methods that rely on molds and heavy machinery, 3D printing enables the creation of intricate designs quickly, cost-effectively, and with minimal waste.
Automakers, from startups to industry giants like Ford, BMW, and Tesla, are investing heavily in 3D printing technology to enhance production efficiency and innovation.
How 3D Printing is Transforming the Automotive Industry
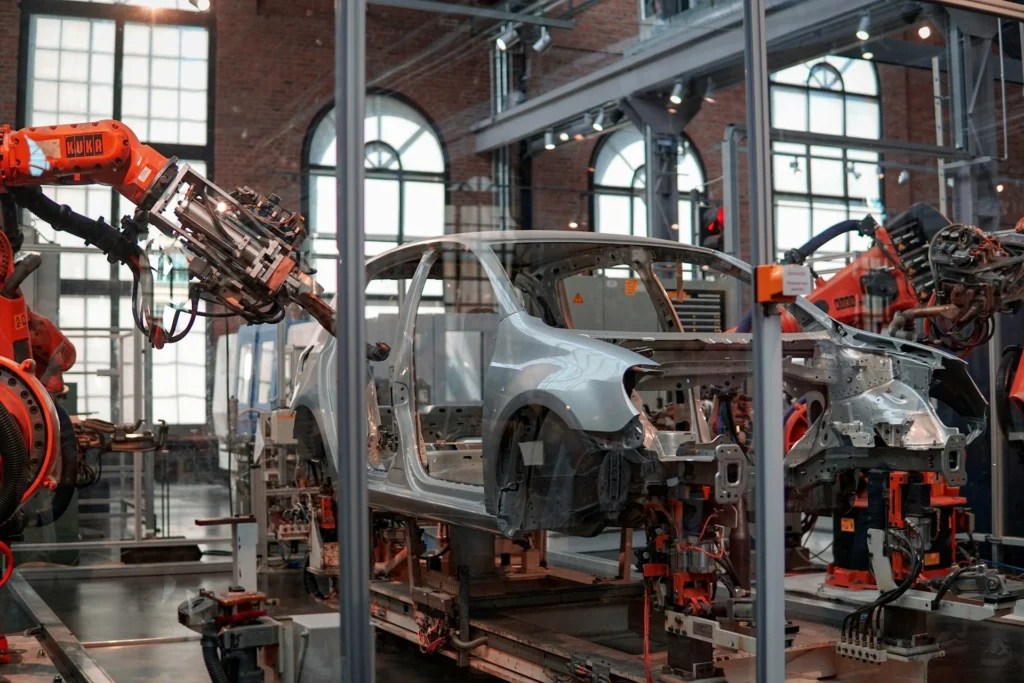
1. Rapid Prototyping and Design Innovation
One of the biggest advantages of 3D printing is rapid prototyping. Car manufacturers can now create design prototypes in days instead of months, allowing engineers to test and refine concepts much faster. This speeds up the development of new models, making the industry more dynamic and responsive to market demands.
- Example: Ford uses 3D printing for prototype development, reducing design cycles and costs significantly.
2. Lightweight and High-Performance Parts
Weight reduction is crucial for improving vehicle performance, fuel efficiency, and electric vehicle (EV) range. 3D printing allows manufacturers to produce lightweight yet durable parts that reduce overall vehicle weight without compromising strength.
- Example: Bugatti used 3D printing to create a lightweight titanium brake caliper, which is both stronger and lighter than traditional cast aluminum versions.
3. Cost Reduction in Manufacturing
Traditional car manufacturing requires expensive tooling and molds. 3D printing eliminates these costs by allowing direct production from digital designs. This reduces material waste, production costs, and assembly time.
- Example: General Motors saved millions by using 3D-printed assembly tools and jigs, which are cheaper and easier to replace.
4. Customization and Personalization
3D printing enables mass customization, allowing automakers to offer personalized vehicles tailored to customers’ needs. Buyers can customize interior trims, dashboard components, and even entire body panels.
- Example: MINI offers 3D-printed personalized car accessories, such as custom dashboard trims and side scuttles, giving customers more control over their vehicle’s design.
5. Sustainability and Environmental Benefits
With increasing pressure on automakers to reduce their carbon footprint, 3D printing presents a sustainable solution. This technology minimizes material waste, lowers energy consumption, and allows for the use of recycled materials.
- Example: BMW is exploring 3D-printed biodegradable materials for interior components, reducing reliance on plastics and other non-renewable resources.
6. On-Demand Spare Parts and Supply Chain Optimization
3D printing has the potential to revolutionize the automotive supply chain by allowing on-demand production of spare parts. This eliminates the need for large inventories, reduces storage costs, and shortens wait times for replacements.
- Example: Porsche uses 3D printing to manufacture spare parts for classic cars, ensuring availability without maintaining large stockpiles.
Challenges of 3D Printing in the Automotive Industry
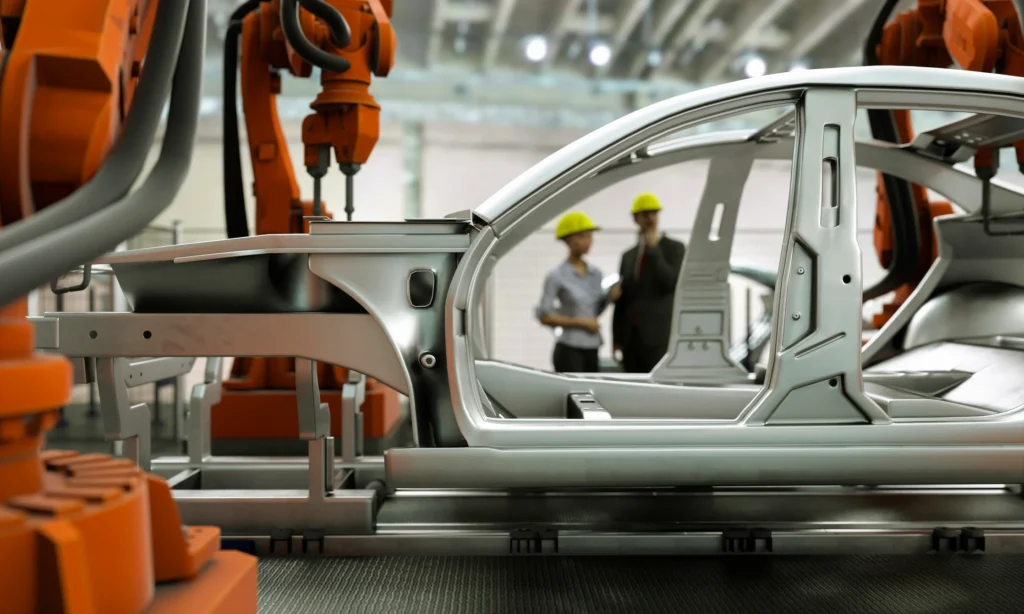
While 3D printing offers numerous advantages, there are challenges that manufacturers need to overcome:
- Material Limitations: Although 3D printing materials have improved, they still need to match the strength and durability of traditional materials in all applications.
- Production Speed: While 3D printing is fast for prototyping, it is not yet efficient for high-volume mass production of larger components.
- Regulatory and Safety Standards: Ensuring that 3D-printed parts meet strict automotive safety regulations remains a challenge.
- High Initial Costs: Investing in 3D printing equipment and training can be expensive for manufacturers transitioning from traditional methods.
The Future of 3D Printing in Car Manufacturing
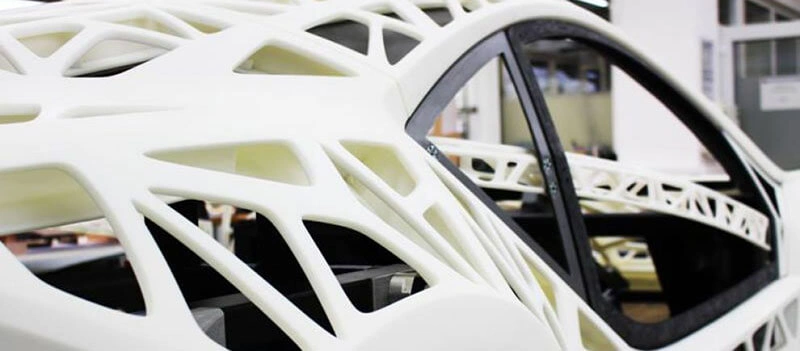
Despite these challenges, the future of 3D printing in the automotive industry is promising. With continued advancements in material science, AI-driven automation, and large-scale printing capabilities, we can expect even greater adoption of this technology.
1. Fully 3D-Printed Cars
Startups like Local Motors have already developed fully 3D-printed vehicles, such as the Strati. While not yet mainstream, this concept could revolutionize car manufacturing in the coming decades.
2. Smarter and More Sustainable Manufacturing
As 3D-printed parts become stronger and more cost-effective, automakers will increasingly adopt this technology to build sustainable, lightweight, and energy-efficient vehicles.
3. Expansion into Electric Vehicles (EVs)
With the rise of EVs, 3D printing will play a crucial role in developing lightweight batteries, aerodynamic designs, and advanced cooling systems to improve performance and efficiency.
Final Thoughts
3D printing is no longer just a tool for prototyping—it is transforming the way vehicles are designed, manufactured, and maintained. From cost reduction and lightweight materials to customization and sustainability, this revolutionary technology is shaping the future of the automotive industry.
As research and development continue, we can expect even greater innovations in 3D-printed vehicles, driving us toward a smarter, more efficient, and more sustainable automotive future. Are you ready to see the next generation of 3D-printed cars on the road?